Making the microchips for our gadgets – with water in mind
We all use multiple semiconductors every day – much of the technology we rely upon can’t function without these tiny chips. But they come at a heavy price. Their manufacture uses hundreds of thousands of gallons of water every day. What does this mean for a water-stressed world?
Semiconductors, often called microchips or chips, are essential components of modern technology that is part of our daily lives. They can be found in mobiles phones, laptops, TVs – and just about every other electrical device you might encounter. But the manufacture of chips comes at a high price, one that we are beginning to pay.
Microchip production needs water
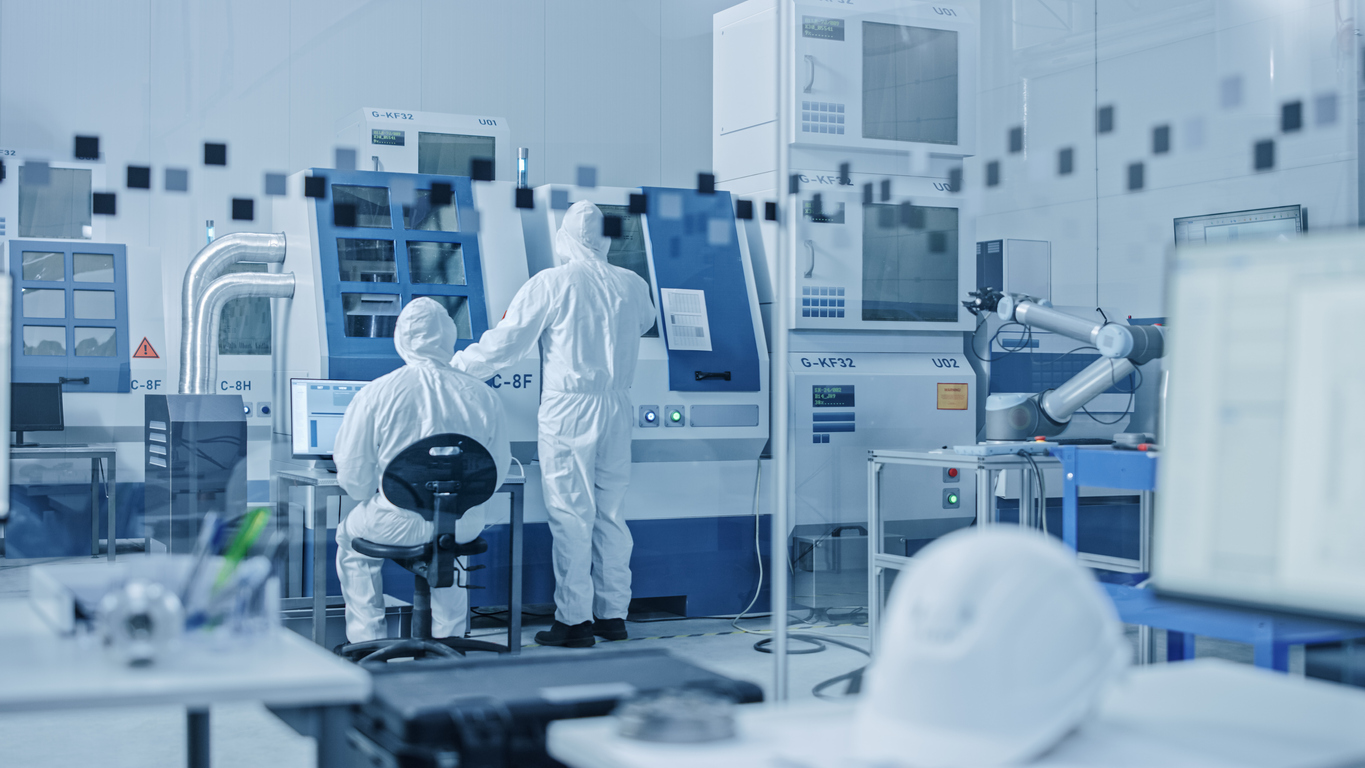
Chips start life as ultra-thin silicon discs, called wafers. The wafers are bombarded with layers of silicon dioxide, metals, and other materials that form the circuit for the chips. After a few layers of material have been spread over the discs, the excess is washed away. This is where water comes in, and it’s not just any water. The water used to wash the wafers must be Ultra Pure Water (UPW) – water that is stripped of every mineral and gas and other possible contaminants – because any trace amount of metal in insufficiently pure water would ruin the chips. Turning ‘normal’ water into UPW uses a lot of energy and produces a lot of wastewater.
This process of layering and washing away is repeated around a hundred times for each wafer, which takes between 12,000 – 15,000 chips. This repeated washing is how Taiwan Semiconductor Manufacturing Co Ltd (TSMC) – which constituted nearly 90% of the market for advanced microchips in 2020 – ends up using more than 150,000 tons of water every day.
What happens when drought hits?
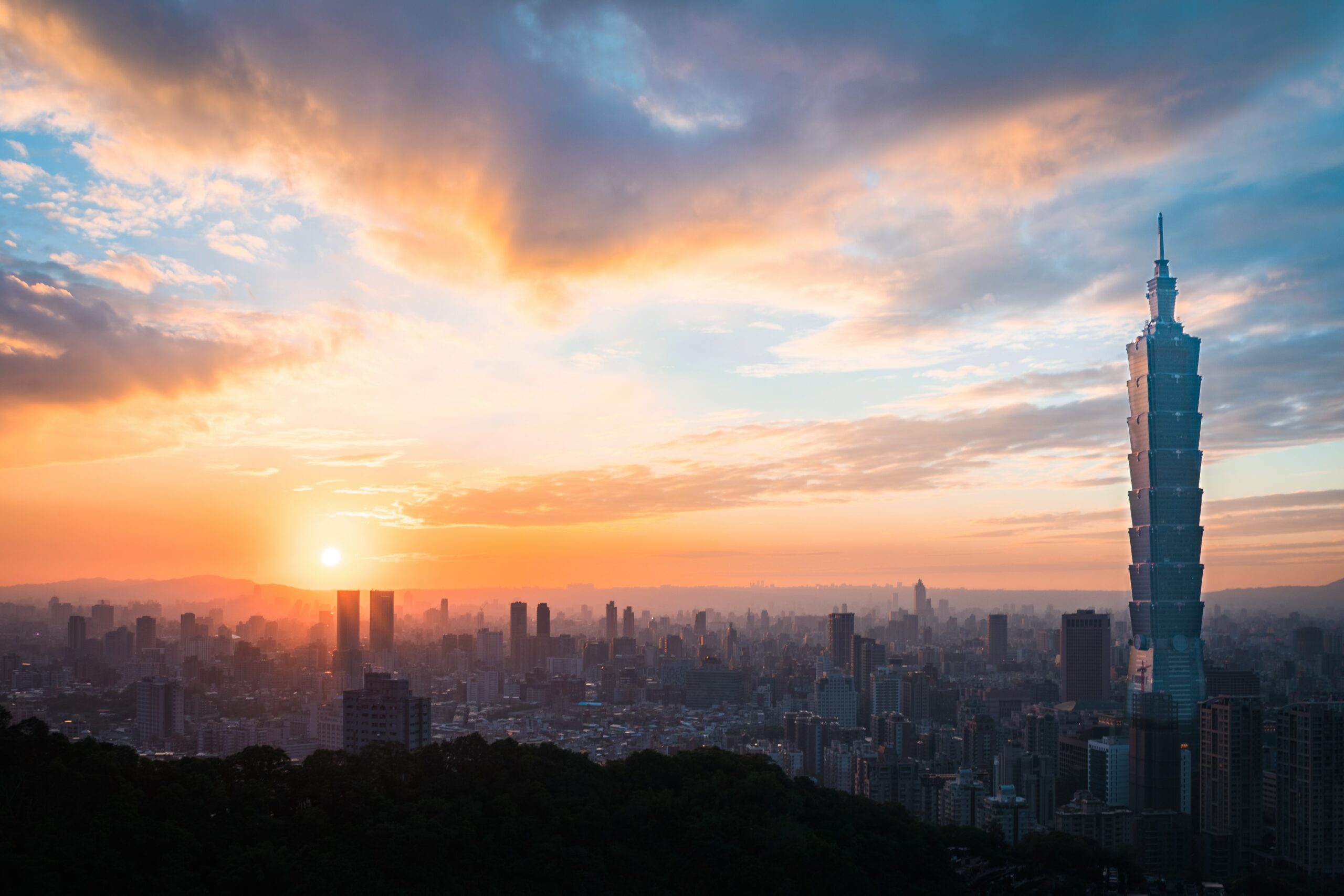
The issue of how much water is used in chip manufacture is amplified when set against the backdrop of a water crisis. Today, nearly a fifth of the world’s population lives in water-scarce regions. This has begun to hit home in Taiwan, the biggest producer of chips: the country makes 60% of the world’s semiconductors.
2020 was an unusual year for Taiwan’s weather. The island is known for being rainy and, usually, it is hit by typhoons in the summer months, which bring huge rainfalls to replenish surface sources and groundwater. But in 2020, there were no typhoons, and rainfall throughout the year was abnormally low. As a result, by 2021 many of the country’s resources were at dangerously low levels, and decisions had to be made about how scarce water resources should be allocated. With semiconductors forming a huge part of the country’s economy, it was no easy question.
At first, the Government worked to protect its semiconductor industry, allocating water resources to the manufacturing sites in preference over farmland. Then, chip producers were asked to reduce their water use by 15%, as water was cut off from the major manufacturing sites for the first time. The factories relied on reserves, and on water transported by tankers from wetter parts of the country.
Water stress affecting manufacturers has impacts further down the supply chain too. In 2020, Apple attributed revenue losses of $6 billion to ‘supply constraints’, reflecting just how hard the chip shortage hit.
And Taiwan isn’t the only place where drought is colliding with the water-heavy chip industry. Arizona is already home to semiconductor factories, but it’s also experienced severe drought, with a water shortage at the country’s biggest reservoir announced for the first time ever in April 2021. With the region already under stress, there are concerns about the potential expansion of chip factories by Intel, and Taiwan’s TSMC.
Can the industry change?
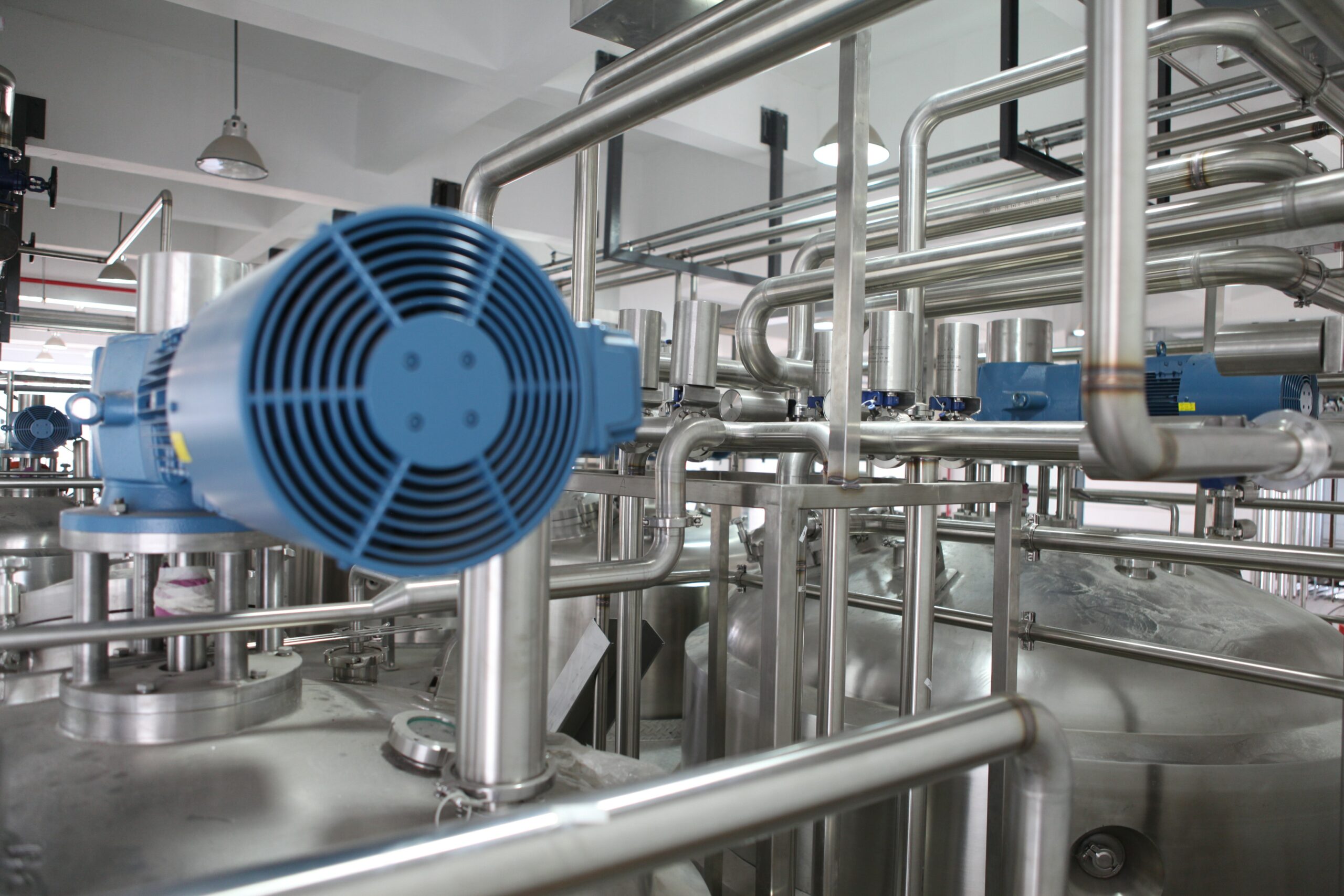
Water waste in the semiconductor industry hasn’t gone unnoticed, and there is growing pressure to find a more sustainable production process.
Fund managers have reported growing demands from investors that the businesses they fund are acting ethically, and working to become ‘greener’. And, as the Taiwanese Government steps have shown, while the economy will certainly remain a priority, ultimately access to water will be cut for chip manufacturers when necessary. In Arizona ,water cuts have been enforced on farmers, with the state currently expecting new chip factories to be built with highly efficient water processes.
These pressures are driving innovation within the industry. Samsung cleans its waste water from chip production, and reuses it in the manufacturing process, claiming to reuse 35% of all its water every day. TSMC, meanwhile, has built a water treatment plant at its factory in Taiwan, which will take industrial wastewater and turn it into Ultra Pure Water.
There’s innovation from outside the chipmakers, too. Gradient is a tech company that has developed wastewater cleaning processes which they claim allow semiconductor plants to recycle 98% of the water they use. Meanwhile, Blue Boson uses patent technology that works at the molecular level to clear water of impurities.
A sustainable future is necessary for progress
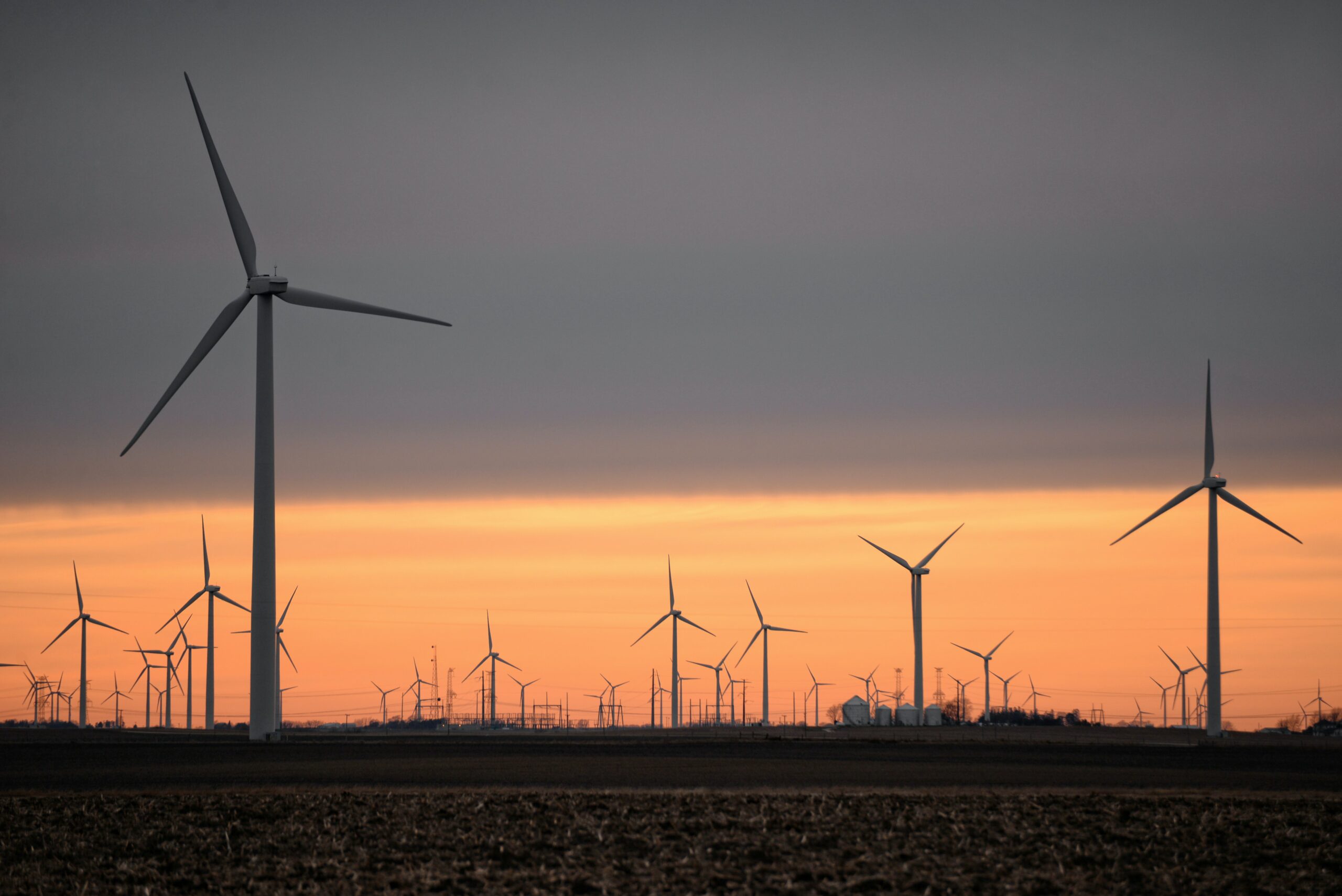
Microchips are contributing to water scarcity, but they are also essential components of the tech that will help us achieve a greener future – present in wind turbine controls, solar panels, and satellites. With increasing pressure from governments, consumers, and investors, the trend towards a more sustainable chip industry will continue, and we can enjoy the promises of this technology.